A Formula 1 race car is designed so that in the event of a crash, individual parts and components can be removed and replaced in mere seconds. The same principles are at play for the Snap, an aerial camera that shoots 4K video, which is made by the Bay Area startup Vantage Robotics. In addition to making the product crash-proof, the assembly technique also makes it highly portable and easily upgradeable. Leave it to an Ideo alum and DARPA Grand Challenge winner to engineer the ultimate camera that flies.
"Aerial video has amazing creative potential, but in our personal experience it was hard and impractical," says Tobin Fisher who founded Vantage with fellow Stanford-trained engineer Joe Van Niekerk in 2013. "It's very analogous to the PC industry in the 1980s. It had the basics, but the implementation required a lot of dedication."
Fisher and Van Niekerk noticed that while there are aerial cameras on the market, they were designed more like drones with a camera attached rather than a camera that's able to fly. The former spoke to a smaller robot enthusiast audience whereas the latter is more consumer-friendly. Meanwhile, the drones that were able to capture the best video were big and cumbersome—a byproduct of the camera stabilization gear and power needed to lift all that equipment into the air—and forced users to program flight paths on their own. Fisher and Van Niekerk's goal? Make an aerial camera that has a built-in director to achieve the most dramatic shots and and tell the best story, and make it easy to use and transport to boot.
To design the aerial camera, Fisher and Van Niekerk mined their past experience. Prior to opening Vantage Robotics, Fisher founded a fuel-cell company and worked in product development at Ideo. "I found that experience especially useful for the balancing act of solving problems that have technical component as well as a human and social component," Fisher says. "It's taking a design approach where the ultimate goal is something a person would value and focusing our technical challenges around user-centric goals. On technical merits, does this achieve a performance goal, like long flight time? On softer merits, it's does look good, feel intuitive, express the magic of flying, or will it be socially awkward?" Van Niekerk also worked in product development at a couple of startups in the action sports industry and at the Volkswagen Electronics Research Laboratory when it won a DARPA challenge for the autonomous vehicle Stanley. He additionally worked on the LIGO project, which proved one of Einstein's theories about gravitational waves by isolating minute vibrations. This was especially applicable for engineering a camera stabilizer that would counteract the motion from flying.
The heart of the design challenge lay in the drone's weight. This impacts its range, how long it can stay aerial, and how robust the design is in terms of surviving a crash. "We spent a week trying to shave off a couple grams on the product," Fisher says. "It's an obsession."
To tackle the weight and impact problem, the designers thought of existing things that are built for lightness and robustness. "We were looking for design analogies and metaphors—people who have solved problems that we can learn from instead of reinventing the wheel," Fisher says.
Formula 1 race cars immediately came to mind. Fisher and Van Niekerk marveled at how these cars would have seemingly disastrous crashes at high speeds, yet the drivers would often walk away unscathed. (Of course, it is very much a dangerous sport and people do die.) Part of this is achieved through the car's construction. It's built to break apart on impact, which distributes kinetic energy sustained from impact. If everything is integrated, then every component needs to absorb the energy created upon impact. To do so, the components need to be more robust which in turn means more weight. The extra weight leads to more momentum in the object, which means more energy generated in a crash.
"That creates a vicious cycle," Fisher says. "The way we could break this cycle was to design the camera to break apart. Then it becomes a virtuous cycle for lower impact energy."
Snap gets its aerial lift courtesy of four propeller blades in a protective carbon-fiber frame, which is based on a Tensegrity structure for lightness and strength. Enclosing the propeller blades—which make 7,000 revolutions per minute—makes then safer and gives users peace of mind when using the camera. "Most drone shots people were getting were [distant] shots," Fisher says. "To tell a great story you need a good subject so having something that could fly a foot from your face is part of that."
The propellers attach to the drone's body with magnets. In the rare case of impact, the drone breaks apart, which distributes kinetic energy thereby reducing damage. Moreover, the magnets make the design modular, meaning that users could upgrade to larger propellers for longer flying distance, unlimited range with a cellular modem attachment, and obstacle avoidance when Vantage makes those available in the future.
The designers selected a Sony Exmor camera and placed it inside a custom-designed, ultra lightweight gimbal stabilizer—a pivoting support that allows rotation around a single axis—to ensure footage isn't shaky. When Fisher and Van Niekerk were researching the highest quality gimbal cameras on the market, they were hovering around three pounds. All told, the Snap weighs 20 ounces, a little more than one pound, and can fly in winds up to 20 miles per hour.
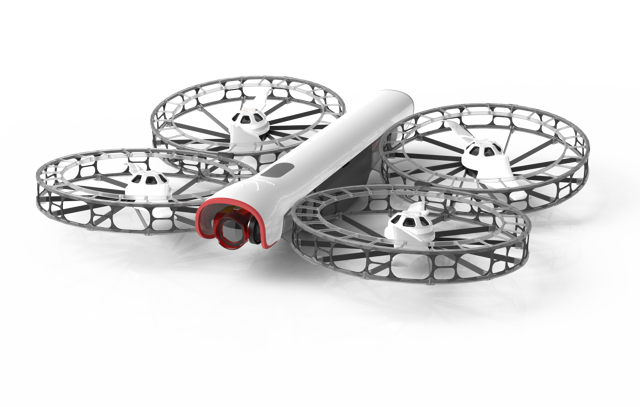
From a software standpoint, the designers developed a tracking system to ensure the drone never strays too far from its user and built a geofence that limits it from going any further than the return travel distance its battery can support. The designers worked with cinematographers to pre-program flight settings that ensure the drone captures the most photogenic and dramatic footage. For example, you can tell the camera to orbit around you on autopilot or fly out and capture a panorama.
The camera is controlled via a smartphone app though users have the option of attaching a gaming controller. The designers embarked on field testing to make sure the UI was easy to use and intuitive. Fisher and Van Niekerk staged their test flights in San Francisco's Golden Gate Park, which is adjacent to the Haight-Ashbury neighborhood. "We had this policy where we would let any passersby who asked about the camera test it," Fisher says. "Many of them happened to be pot dealers." They figured if stoners could understand the product and the product could withstand their use—"That's really stress testing," Fisher quips—they hit their mark on creating an intuitive and physically strong design.
"The end goal is just to make the most amazing videos possible," Fisher says.
Snap, at $895 plus $20 shipping, is available for preorder from vantagerobotics.com. The first beta shipments are due out in July and subsequent shipments in August and September.